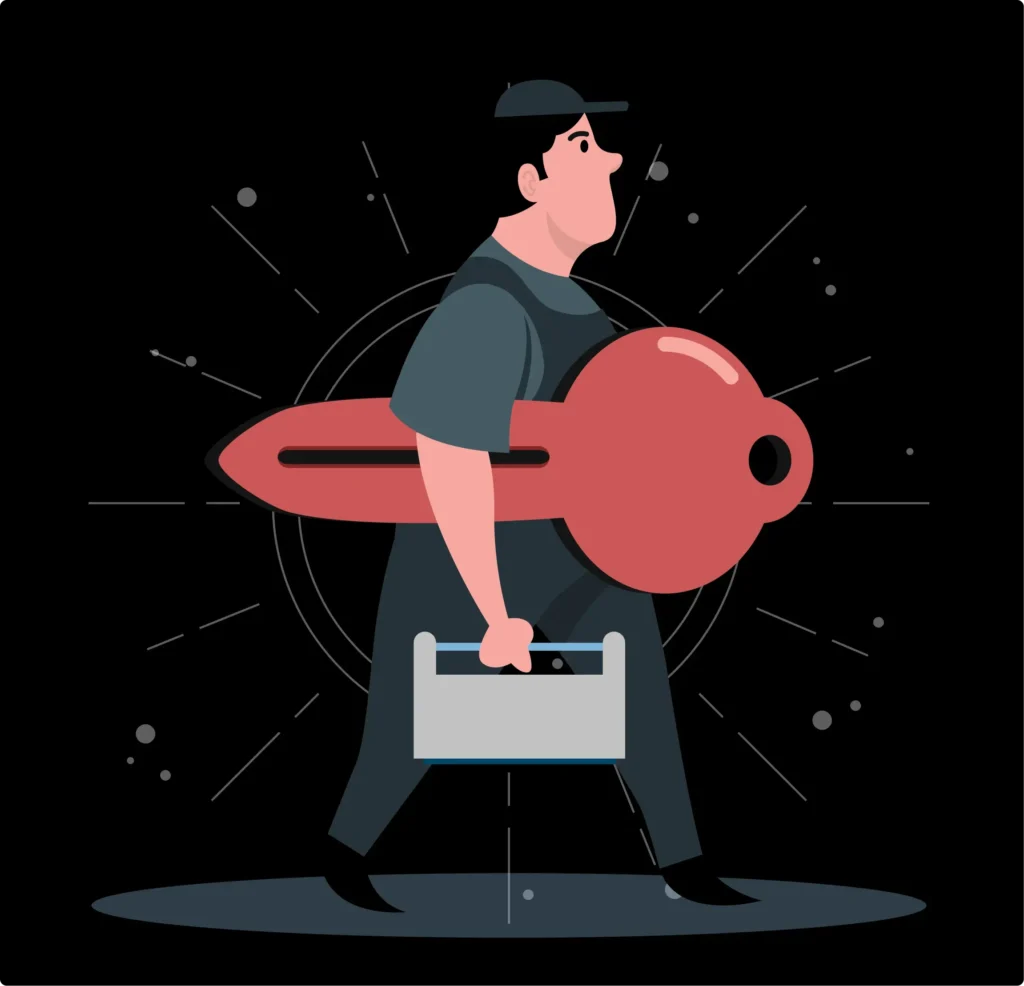
- One should prioritize accuracy over rushing through tasks.
- Mastering schematic & conducting an isolation diagnosis is non-negotiable.
- Static pressure checks & airflow inspection directly impact customer satisfaction.
- Technicians should understand a customer’s issue clearly.
- Staying clean & prioritizing safety help technicians build repeat business.
An HVAC technician’s work is characterized by its physical demands. In 2025, being an HVAC tech means taking on responsibilities beyond servicing air conditioning units or installing heat pumps. You need to apply your intellect along with unmatched speed and efficiency. The introduction of new energy efficiency regulations, the growing trend of customers seeking immediate service, and the adoption of smart HVAC systems as replacements for traditional heating and cooling units compel technicians to adapt to them or risk obsolescence.
75% of homeowners prefer energy-efficient HVAC systems, and failing to provide a suitable recommendation results in losing clients. Modern HVAC equipment forces technicians to diagnose and repair systems more efficiently than traditional methods. Although 81% of HVAC service calls originate from repeat customers, many HVAC technicians neglect to maintain an appropriate service log, which incurs substantial revenue losses. Emergency calls are increasing, but poor scheduling results in delayed responses, dissatisfied customers, and negative reviews. Using service agreement software like ZenHVAC not only helps HVAC companies navigate these problems but also improves the profitability and operations of their business more than ever.
This guide offers eighteen essential tips for HVAC technicians to consider in 2025, covering everything from thoroughly understanding your customer’s issue to visually inspecting the airflow and ductwork, as well as maintaining effective communication with the team.
Table of Contents
Tip 1: Understand Your Customer's Issue
Ask the customer for symptoms, such as ” Is the system blowing warm air instead of cool air? Is there a strange noise or smell? Has any reprogramming of the thermostat taken place recently? Any power outages? ” If that is not enough, look at the maintenance history to check if similar complaints have been received in the past. You are the HVAC tech, not your customer, and it is normal for them to struggle to explain the problems related to their heating and cooling system. Take the time to ask all the details and questions while putting yourself in their shoes. This will also help you troubleshoot the issue more precisely and efficiently.
Tip 2: Look at How The Specific System Is Wired
You should not consider the task of installing an HVAC unit as a copy-and-paste job. Just because the system is brand new doesn’t mean that installing it won’t cause any issues. The requirement for an HVAC unit varies depending on the job site and the specific location, as each might have different environmental needs. You might have to change the internal wiring configurations, such as fan speed, staging, and jumper pin settings on control boards, based on the setup and size of the unit. Most HVAC units have multi-tap transformers to work with various voltage supplies, and if they are tapped incorrectly, this might result in chattering relays and premature equipment failures. Furthermore, just because the system is brand new doesn’t mean that there won’t be any faults. Misconfigured settings and loose wiring might occur due to shipping failures.
Tip 3: Understand The Schematics Of The HVAC Unit
Schematics can seem quite intimidating to look at, and it’s a common reaction to avoid such diagrams. However, even though it might seem daunting at first, schematics can actually be enjoyable to learn. But here’s a reality check: clients and employers will always prefer technicians who can diagnose and manage complex HVAC issues with confidence. It’s fine to watch tutorials and read books on understanding schematics to make the best use of them, but real progress will only come from examining schematics regularly. Familiarizing yourself with them will help you identify components, trace circuits, and diagnose issues more quickly and accurately over time. Another advisable practice is to open up the HVAC units and review their wiring diagrams pasted on the panel during inspections or downtime, especially in commercial settings.
Tip 4: Do Isolation Diagnosis
Isolation diagnosis is all about finding and separating the main cause behind the problem that has occurred in the HVAC system. For example, if the blower isn’t functioning, is it the capacitor, the motor, the relay, or the control board? You need to isolate each component and conduct tests. Many technicians may hesitate to do this, thinking it requires extensive permutations and combinations, but that’s not the case. Each time you test a component, a manageable number of possibilities remain. Furthermore, replacing the wrong item will cost money and time, and will put you on the list of giving bad customer service. So, doing an isolation diagnosis helps you become a reliable technician as well as gain customer trust.
Tip 5: Learn Refrigerant Management Thoroughly
Technicians should always check for cracks in heat evaporator coils, condensing units, and refrigerant lines, and repair leaks before charging with refrigerant. There are additional factors to consider, such as using compatible refrigerants to avoid damaging the system, and ensuring the right amount of refrigerant is added- not too much or too little- to prevent strain on the compressor and heat exchanger. Furthermore, technicians should recover refrigerants during repairs and avoid releasing harmful gases into the environment, as this poses risks to both homeowners and their health.
Tip 6: Perform a Through Evacuation Process
Most technicians either skip the evacuation process or do it in a rush and miss important steps involved in the evacuation process. Performing a thorough evacuation will remove the contaminants, moisture that can cause corrosion, acid buildup, or refrigerant breakdown, and air, which forces the system to work harder. No customer would want to purchase expensive components like compressors and valves that are damaged by moisture and contaminants, especially when such issues could be avoided with a proper evacuation process.
By using larger hoses, micron gauges, and the advanced tools available today, there’s no excuse for technicians to fail at proper evacuation.
Tip 7: Always Measure The Static Pressure
Many HVAC technicians believe that measuring total external static pressure is sufficient. However, to identify issues in the airflow, measuring the static pressure is the most effective method available. Install the positive and negative pressure probes on the supply and return sides of the ductwork, respectively. If the return static pressure is high, it indicates that either the duct is undersized or the filter is dirty, and if the supply static pressure is high, then the ductwork is undersized. In either case, one must resize the duct or clean the system to achieve the appropriate total external static pressure (TESP) and airflow distribution.
Tip 8: Have a Well-Stocked HVAC Toolkit
Technicians should always be ready for any kind of complex jobs that come their way on a particular day. Arriving at a client’s home and discovering that you are missing the tools required to install or repair the HVAC unit is problematic. Every HVAC technician must have screwdrivers, pliers, wrenches, a refrigerant leak detector, a thermal imaging camera, a LOTO device, vacuum pumps, saws, drills, a voltage detector, and a tape measure to service any HVAC unit.
Tip 9: Visually Inspect The Airflow And The Ductwork
A well-designed air conditioning unit, furnace, or heat pump relies on proper airflow to efficiently deliver cool or heated air. Blocked airflow results in poor performance, regardless of how advanced the HVAC system may be. If your customer complains about certain rooms being excessively hot or cold, a malfunctioning compressor, blower motor, or heat exchangers, higher energy bills, and the premature failure of evaporator coils and the condensing unit, then the cause is often air blockage.
If you are providing maintenance services, be sure to change the air filters. Additionally, advise customers to replace filters every one to three months, particularly during peak season. A dirty filter restricts airflow. Check for dust buildup, collapsed ducts, and disconnected sections in the ductwork. Seal any leaks in the ducts to reduce energy waste from escaping air. Properly insulate the ducts to maintain a balance in both heating and cooling. Ensure that no furniture, curtains, or rugs are blocking the vents, and encourage homeowners to keep their vents open to improve airflow distribution. Clean dirty blower fans and adjust the fan speed to make sure that there is proper airflow with minimal effort from the HVAC unit
Use Manual J calculations to accurately size a system for a home or business, since a large AC unit may cool quickly but will not effectively remove humidity. Similarly, an undersized air conditioner will run continuously, leading to increased wear and tear on the system. Ensure appropriate ventilation settings, as negative air pressure allows contaminants, moisture, and odors to enter from outside, while positive air pressure can lead to air leaks and energy waste.
Tip 10: Make Sure There Are No Wire Abrasions
Most major failures in control circuits occur due to minor abrasions. Always check for frayed insulation, exposed copper, melted or discolored insulation, and wires rubbing against sharp edges, metal parts, or moving components in the condensing unit and air handler or furnace unit. If you find any damage, reroute the wiring to avoid contact with sharp edges and use grommets, conduit, or loom tubing for protection. When crimping or clamping, ensure there are no loose connections.
If you suspect an abrasion but it is not visible, use an insulation resistance tester to check the wiring.
Tip 11: Clean The Drain Pipes And Pans Properly
A clogged drain line can cause water buildup, promoting potential mold growth. The best way to clear the drain and eliminate the blockage is to access the area beneath the evaporator coil and clean the hard-to-reach spots with thin brushes. Most of the time, misdiagnosed issues are the cause of cracked drain pipes.
Tip 12: Test All Modes Of Operation
It is understandable that no one wants to run a system in cooling mode in sub-zero temperatures. It’s freezing cold outside, and why would anyone run the system in cooling mode when the customer won’t need it for the next several months? But what if it fails when the customer needs it? They won’t enjoy having to call for service to fix the non-functioning unit when they really need it. That’s frustrating for both you and your customer. The same applies to humidifiers as well. Ensure that they can also dehumidify if they perform both functions.
Tip 13: Do not Rush To Finish The Job
There’s no need to rush immediately after finishing the job. Once the maintenance, repair, or installation is complete, run the air conditioning system or heating unit through a full cycle to ensure all components are functioning correctly. Check the temperature difference between the supply and return air to confirm proper operation. If the unit stops before completing a full cycle, ask your customer to verify if their thermostat caused the interruption. If not, troubleshoot the underlying issue; if you can’t resolve it, don’t hesitate to call for help and reach out to your HVAC contractor. The last thing you want is for your customer to leave a low rating.
Tip 14: Make Safety a Priority
HVAC jobs involve many safety hazards, from working with electricity to handling pressurized refrigerants. Common hazards include electric shock due to faulty wiring, exposed circuits, or improper grounding; skin burns and respiratory issues from leaking refrigerant tubes; and falls and injuries from working on rooftops, ladders, and in tight spaces.
You should always wear gloves, safety goggles, masks, and steel-toe boots. Test electrical components before touching them, dispose of refrigerants safely, and use safety harnesses when working at heights.
Tip 15: Call For Help If You Get Stuck During Diagnosis
If you are an HVAC apprentice, you will want to prove yourself as fit for this work. You would review all the details, conduct thorough troubleshooting, address the issues, and put forth your best effort in service. Still, there may be something you are overlooking, and you might not understand why. It’s completely fine; make sure to explain everything you have done so far to the customer and the HVAC company you work for, and request additional troubleshooting from your seniors. If you are already an experienced HVAC technician, it may take a hit to your pride to ask for help, but you shouldn’t provide a false diagnosis to your customer just because of that. It won’t benefit anyone, and you wouldn’t want your client to leave a low rating and negative review due to poor service.
Tip 16: Maintain Effective Communication With Your Team
Even though it is the responsibility of the owner or manager of the HVAC company to establish a proper structure for efficient communication both within the team and with the manager, you can also share in this responsibility. For instance, deciding whom to call when the client is not at home or when a client cancels the service after you arrive, as well as determining which activities will affect your to-do list, among other tasks. The ZenHVAC app provides features like scheduling and dispatching, enabling technicians to use their phones to show their real-time location and report what services they have provided and to whom. Ultimately, maintaining this kind of communication will rely on the people in the back office.
Tip 17: Appear Clean Before Your Customer
As an HVAC technician, you will mostly work inside people’s homes. If you are sweaty and muddy and leave marks and footprints everywhere, it will make the client uncomfortable, disrespected, and anxious about their property. Moreover, a customer will analyze your work from your outfit. If you show up to their home dirty, it will reflect that you are not capable of giving quality service, even before you start. Keep your truck organized and even keep an extra clean uniform in it for emergencies. After you are done servicing, clean the mess before you leave the house, and make sure everything is in place just the way it was before you arrived.
Tip 18: Focus On Customer Satisfaction
Building strong relationships with customers can lead to long-term loyalty and repeat business. Providing customers with estimates for your service will help identify the factors affecting the overall costs. Educate them. Use diagrams and photos to help customers understand the issues with their HVAC units and provide them with recommendations based on that. These customers are likely to call back for service again because they will know the overall maintenance of their HVAC unit.
Moreover, use straightforward and non-technical language to help them understand the complex HVAC issues. Use the free SEER calculator to explain the energy savings they can gain from new appliance installation. Explain the advantages and disadvantages of the solutions you are providing. Finally, call or text after the service to confirm if the system is functioning well. This will enhance their trust in you.
Conclusion
Being an HVAC technician in 2025 requires skills in repairing and installing heating and cooling systems, along with the technical knowledge to keep up in an ever-changing industry. This includes everything from troubleshooting techniques to tool selection and being clean. Any technician who continuously hones their skills will always be a preferred choice. The best HVAC tech is marked by good communication and a keen focus on safety.
ZenHVAC is a service agreement software designed for HVAC contractors looking to operate more efficiently. With features such as scheduling and dispatching, estimates and proposals, timecard management, automated invoicing, and CRM, both managers and technicians can easily track the service history of their clients digitally, reduce fuel costs with GPS tracking in the dispatching solution, and avoid double appointments through effective scheduling. Additionally, service calls, maintenance record tracking, and sending estimates are handled with instant efficiency, resulting in happier customers and a smoother workflow.
Are you ready to elevate your HVAC company to the next level? Schedule a free demo with ZenHVAC and explore the potential of tomorrow’s HVAC service management for yourself.
Get Insights Delivered Straight
To Your Inbox!
Related Reading
Why Your Field Software Management Software Needs QuickBooks Integration
ZenTrades Why Your Field Service Management Software Needs QuickBooks Integration Read More Request Demo...
Read MoreZenTrades How To Manage Electrical Service Agreements Like...
Read MoreZenTrades The Best 5 Jobber Alternatives In 2023...
Read More